, 29.11.2019, 15:27
Gedruckte Wirklichkeit - Erfahren Sie mehr über das Selektive Lasersintern
Der thyssenkrupp Testturm und das thyssenkrupp TechCenter Additive Manufacturing machen gemeinsame Sache. Da kann ja nur etwas ganz Besonders bei herauskommen: Der erste Testturm im Miniaturformat zum Mitnehmen - hergestellt im top-modernen Selektiven Lasersinter-Verfahren.
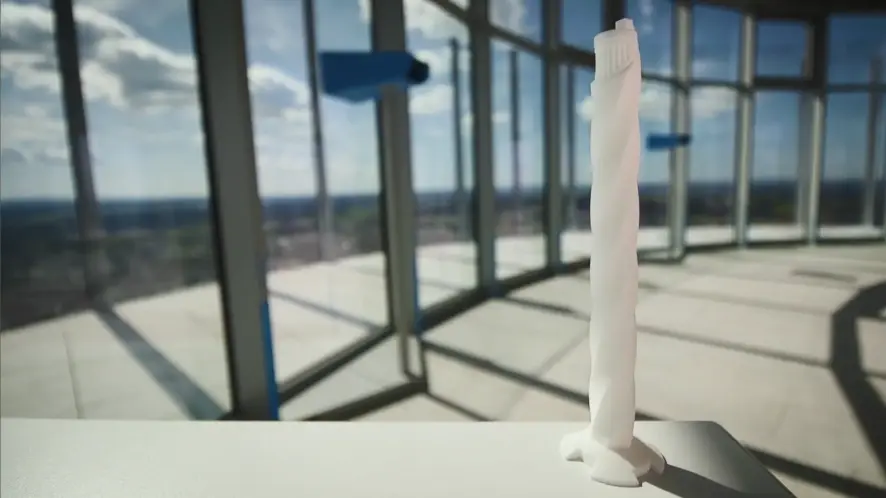
Die Idee
Die Teams von zwei der innovativsten Bereiche der gesamten thyssenkrupp Gruppe schlossen sich für dieses Projekt zusammen. Während im thyssenkrupp TechCenter Additive Manufacturing in Mülheim an der Ruhr mit den modernsten Fertigungsverfahren die Produktion der Zukunft optimiert wird, werden im thyssenkrupp Testturm in Rottweil Aufzüge entwickelt, die die Personenbeförderung der Zukunft revolutionieren.
Da der Testturm gleichzeitig die höchste Besucherplattform Deutschlands auf 232 m bietet, fanden sich die Teams beider Unternehmensbereiche zusammen, um für die Tausenden Besucher pro Jahr ein außergewöhnliches Andenken zu produzieren: Den ersten im Selektiven Lasersinter-Verfahren (SLS) hergestellten Mini-Testturm. Weiß, wie das Original bei schönstem Sonnenschein, aber dabei nur 12,8 cm hoch, während es das echte Bauwerk auf 246 m bringt und dadurch auch den Spitznamen ,,höchster Wolkenkratzer Baden-Württembergs" bekommen hat. Sehen Sie hier das ausführliche Video über unseren Testturm-zum-Mitnehmen.
Das Verfahren
Beim SLS wird ein Pulver mit Hilfe eines Lasers selektiv geschmolzen und somit Schicht für Schicht ein Bauteil aufgebaut. Das Besondere ist, dass der komplette Bauraum des Druckers Schicht für Schicht mit Pulver gefüllt wird und somit das restliche, nicht geschmolzene Pulver im Raum verbleibt und das geschmolzene Teil trägt. Dadurch ist der Quader quasi komplett nutzbar. Hochpräzise Bauteile können, unabhängig von der Schwerkraft, in den dreidimensionalen Raum gelasersintert werden. Dadurch ermöglicht das Verfahren die Fertigung komplexer, ineinander verschachtelter, sogar innen strukturierter Bauteile, die in klassischen Verfahren in einem Produktionsschritt so nicht möglich wären. Und das ganz ohne Werkzeuge, nur auf Basis einer digitalen Zeichnung. Eine Chance für die moderne und nachhaltige Fertigung von herausfordernden Komponenten bspw. für die Luft-und Raumfahrttechnik, die Automobilindustrie oder die Medizin.
Schon die aus Kunststoff gesinterten Teile weisen eine sehr hohe Belastbarkeit und Beständigkeit auf. Beim Selektiven Lasersintern wird aber auch mit Metallen wie bspw. Aluminiumpulver gearbeitet. Während der Laser das Pulver schmilzt, entstehen dabei im verglasten Bauraum beeindruckende Funken und Spritzer, die aber in der Regel leider nur die Ingenieure vor Ort zu sehen bekommen. Um dieses hochmoderne Verfahren auch nach außen zu präsentieren, hat thyssenkrupp TechCenter Additive Manufacturing ein Video veröffentlicht, das die wichtigsten Schritte zeigt.
Das SLS ermöglicht es uns, kleinste Details und feinste Strukturen herzustellen, was man am Beispiel unseres Miniatur-Testturms sehr schön erkennen kann.
In hauchdünnen Schichten, dünner als ein Blatt Papier, wird das Pulver vollflächig am Boden des vorab bereits erhitzten Bauraums ausgebracht. Auf Basis der Konstruktionszeichnung wird nun der gewünschte Bereich gelasert und das Pulver dort geschmolzen. Anschließend senkt sich die Plattform ab, und die nächste Pulverschicht wird aufgetragen. Dabei sind die Schichten so dünn, dass sie anschließend kaum noch erkennbar sind, im Gegensatz zum breiter bekannten herkömmlichen 3d-Aufbau-Druck. Schicht für Schicht entsteht so das gewünschte Teil. In unserem Fall wurde der erste Original thyssenkrupp Testturm im Miniaturformat in über 1.000 Schichten gelasersintert. Anschließend werden die Bauteile aus dem Pulverblock entnommen. Das nicht genutzte Pulver wird am Ende des Vorgangs wiederverwertet, sodass dieses Verfahren als besonders ressourcenschonend gilt.
Selbstverständlich wurde das filigrane, 3D-gedruckte Modell des Rottweiler Testturms nach den Originalentwürfen der weltweit bekannten Architekten Werner Sobek und Helmut Jahn gefertigt.
Die Zukunft
Das SLS ist ein Verfahren des sogenannten Additiven Manufacturings, also verschiedener werkzeugloser Fertigungsprozesse, bei denen Material auf Basis von digitalen Zeichnungen Schicht für Schicht aufgetragen wird, um ein Bauteil zu produzieren. Im Gegensatz dazu stehen die subtraktiven oder abtragenden Verfahren, wie bspw. Drehen oder Fräsen, bei denen Material abgetragen wird.
In diesem modernen additiven Verfahren gibt es fast unbegrenzte Design- und Individualisierungsmöglichkeiten. Es wird, bspw. durch Netzstrukturen, so wenig Material wie nötig für das Bauteil verbraucht, was der Umwelt zu Gute kommt und auch generell den Leichtbau neuer Produkte enorm vorantreibt. Die Produktion von Prototypen wird verkürzt und günstiger, da keine Werkzeuge mehr anfallen. So hat das thyssenkrupp TechCenter Additive Manufacturing auch einige Muster für mögliche Handläufe mit Brailleschrift für unseren innovativen MULTI-Aufzug getestet und im SLS angefertigt.
Das Ergebnis
Die mit 572 Stück limitierte Erstauflage des SLS 3D-Testturms mit Seriennummer ist ab sofort sowohl im Testturm in Rottweil also auch online im Testturm-Shop für 25 Euro pro Stück erhältlich.
Zahlen und Fakten Mini-Testturm
Erstauflage 2019: 572 Stück mit Seriennummer
Höhe: 127,94 mm
Maßstab: 1:1.923
Gewicht: 15 Gramm
Material: technisches Thermoplast Polyamid 12
Info: thyssenkrupp TechCenter Additive Manufacturing
Im thyssenkrupp TechCenter Additive Manufacturing bündeln unsere Kollegen als Herzstück eines agilen Start-ups ihre Kompetenz. Mit hochmodernen Industriedruckern für Metalle und Kunststoffe stellen sie dort sicher, dass Kundenwünsche - egal ob Funktionsmuster oder Serienproduktion - auf Industrieniveau mit entsprechender Qualität und Reproduzierbarkeit gefertigt werden können. Unsere Kollegen waren von der ersten Idee über die Planung bis hin zur Realisierung unseres Mini-Testturms engagiert an unserer Seite.
Fun Fact
Der größte bisher im Selektiven Lasersinter-Verfahren hergestellte thyssenkrupp Testturm ist 1,85 m hoch und besteht aus 5 miteinander verschraubten Einzelteilen. Wenn er nicht gerade auf Messen zu sehen ist, steht er in der thyssenkrupp Elevator Konzernzentrale in Essen.