, 2019-11-29, 03:27 PM
Printed reality - The test tower you can take home with you
The thyssenkrupp test tower has teamed up with thyssenkrupp TechCenter Additive Manufacturing to create something extraordinary: the first scale model of the test tower you can take home, manufactured using an ultra-modern process called selective laser sintering.
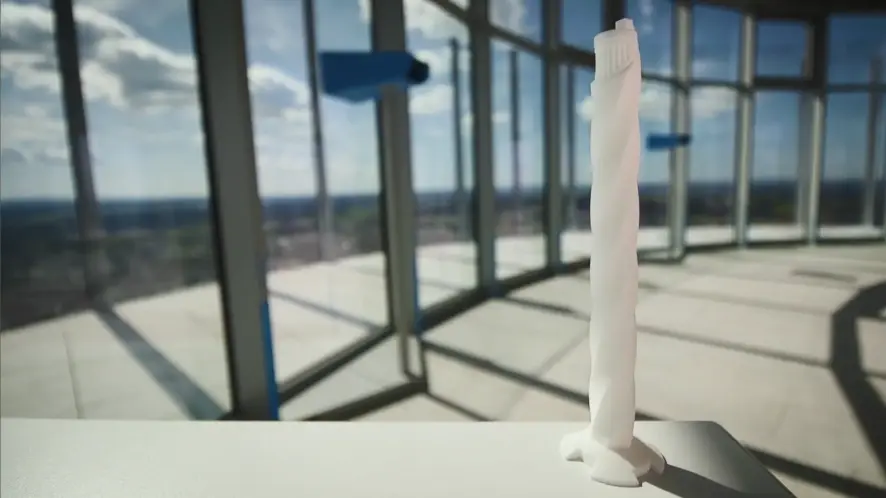
The idea
This project brought together teams from two of thyssenkrupp Group's most innovative divisions. Staff at the thyssenkrupp TechCenter Additive Manufacturing in Mülheim an der Ruhr use cutting-edge manufacturing processes to perfect the industrial production systems of tomorrow, while the thyssenkrupp test tower in Rottweil develops elevators that are revolutionising urban mobility.
As the test tower has become a major tourist attraction, welcoming thousands of visitors a year, the two divisions decided to work together to produce a very special souvenir - the first mini test tower to be made using selective laser sintering, or SLS. The model is just as white as the real tower on a sunny afternoon, but stands at only 12.8 cm (5 inches) high, whereas the full-size structure is 246 m (807ft) tall and has been dubbed 'Baden-Württemberg's tallest skyscraper'. Watch our video about the special 3D-rpint of our test tower here.
The process
In the SLS process, powder is selectively melted using a laser, allowing components to be built up layer by layer. What makes it so special is the fact that the printer's whole construction compartment can be filled with powder layer by layer, with the non-melted powder staying in the compartment and acting as a base for the molten component. This means that virtually the entire layer of powder is used during manufacturing. High-precision components can be laser-sintered in three dimensions without having to take gravity into account. This in turn means that the process can be used to produce complex, inter-locking components, including components with their own internal structures, in a single step, in contrast to multi-stage traditional processes. And it's all done purely on the basis of a digital drawing, with no tools whatsoever. SLS represents a huge opportunity to establish modern, sustainable manufacturing processes for high-performance components in industries like aerospace, medicine or the automotive sector.
Plastic parts made using the sintering process are impressively strong and durable, but SLS can also be used with metals, including powdered aluminium. As the laser melts the metal powder, it produces an impressive display of fireworks in the manufacturing chamber. Unfortunately though, the engineers on site are usually the only ones who get to see them. To help the outside world understand exactly how this ultra-modern process works, thyssenkrupp TechCenter Additive Manufacturing has made a video showing the key stages of fabrication using SLS.
Thanks to SLS, we can manufacture incredibly precise structures down to the smallest detail - as you can see from our mini test tower.
First, the powder is spread out in ultra-thin layers, thinner than a sheet of paper, over the whole floor area of the pre-heated construction chamber. Next, the powder in certain areas is lasered and melted to match the design in the technical drawings. Finally, the platform drops down and is replaced by the next layer of powder. Unlike conventional 3D printing, the layers in the SLS process are so thin that they are virtually impossible to spot on the finished product. Each part is built up gradually, layer by layer; the miniature test tower is made up of over 1,000 laser-sintered layers. Once manufacturing is complete, the finished parts are removed from the powder cake. Any unused powder is reused or recycled at the end of the process, making this method of manufacturing a highly efficient way of using resources.
Of course, our highly-detailed 3D model of the Rottweil test tower is based on the original architects' drawings by renowned architects Werner Sobek and Helmut Jahn.
The future
SLS is an example of so-called 'additive manufacturing'. The term is used to refer to a range of manufacturing processes in which components are produced by layering materials on top of each other without using tools. This is in contrast to traditional subtractive or ablative processes like turning or milling, where material is cut away to produce the desired shape.
This modern, additive process holds out the prospect of almost limitless design freedom and customisation. For example, its use of network-like structures means that components can be built using the bare minimum of materials, which is good for the environment and represents a huge step forward for lightweight manufacturing. And since tools are no longer required, producing prototypes has become faster and cheaper, too. For instance, thyssenkrupp TechCenter Additive Manufacturing also used SLS to produce some handrail prototypes for testing purposes for our innovative MULTI elevator, complete with labels in Braille.
The result
The first edition of the SLS 3D test tower, limited to 572 individually-numbered pieces, is available now at the test tower in Rottweil or in the test tower online shop. The models are priced at 25 euros each.
The mini test tower at a glance
2019 first edition: 572 individually numbered pieces
Height: 127.94 mm (5 inches)
Scale 1:1,923
Weight: 15 grams
Material: Polyamide 12 technical thermoplastic
Info-box on thyssenkrupp TechCenter Additive Manufacturing
The thyssenkrupp TechCenter Additive Manufacturing brings together the combined expertise of our colleagues to create an agile start-up with our people at its heart. The TechCenter's staff use cutting-edge industrial printers for metal and plastic to meet our customers' demanding requirements. Whether they need a single prototype or a mass-produced component, the TechCenter is there to make sure they get a high-quality, highly-reproducible product suitable for industrial use. Our colleagues from the TechCenter were at our side every step of the way, from initial planning right through to the first mini test towers leaving the production line.
Fun Fact
The biggest model of the thyssenkrupp test tower we've managed to make so far using SLS is 1.85 m high and made up of 5 separate parts screwed together. When it's not on tour at various trade fairs, you can find it at thyssenkrupp Elevator Group Headquarters in Essen.